某机匣无人值守技术研究
发布时间:2021-03-22所属分类:计算机职称论文浏览:1次
摘 要: 摘要:该文以某对开机匣为载体,以实现零件无人值守加工为研究目标,从数控程序的编制、优化、防错、零件的毛坯状态控制、刀具管理、工装管理、工装的装夹与找正、加工前的刀具准备、刀具的机内对刀测量以及零件的在线测量技术方面展开研究和论述。最终建立
摘要:该文以某对开机匣为载体,以实现零件无人值守加工为研究目标,从数控程序的编制、优化、防错、零件的毛坯状态控制、刀具管理、工装管理、工装的装夹与找正、加工前的刀具准备、刀具的机内对刀测量以及零件的在线测量技术方面展开研究和论述。最终建立起了一套适合对开机匣零件数控加工的机床高效应用模式,为后续自动化生产线建设提供技术支持。
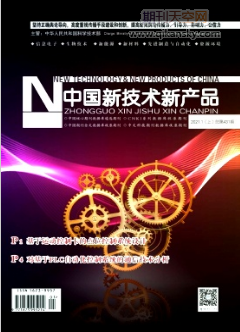
关键词:数控加工;在线测量;机内对刀
0引言
近代飞行能力的每一次突破,都与推进技术的发展直接相关,航空发动机由于研制难度高等特点,被誉为是“现代工业皇冠上的明珠”[1]。航空发动机产业链长,覆盖面广,涉及机械、材料、电子和信息等诸多行业,对基础工业和科学技术的发展有巨大带动作用和产业辐射效应[2]。
目前,数字化制造方面在工厂已经具备了良好的建设条件,也为航空发动机的先进制造提供了保障。例如计算机网络办公全面普及,满足信息技术应用。计算机辅助设计与制造(CAD/CAM)、产品数据管理系统(PDM)、制造执行系统(MES)等系统应用普及,建立了基础数据库,具备良好的数字化制造基础。先进的高速高效数控加工设备,可以实现产品制造的快速反应。数控加工自动编程、机匣高效加工技术和计算机几何仿真技术具备了数字化制造的技术能力。对柔性制造单元的配置有了深入的了解。以上基础条件和技术储备就是为了实现传统制造向数字化制造转变。
该项目从刀具、虚拟制造技术(切削参数)、在线测量、机内对刀、机床的维护、工装的管理和加工流程等方面进行了系统性的开发及研究,建立起了一套适合对开机匣零件数控加工的机床高效应用模式。该机床综合应用方案涉及的技术及管理方案符合工厂大部数控加工中心的使用要求,随着该机床使用技术的推广,成熟度提升,可以逐渐改变机匣厂自动化加工生产能力,有效地提高机匣铣加工效率及零件加工质量,尽可能地减少现场操作者对零件加工状态的干预,保证现场零件加工的一致性,实现精铣高效加工,为后续的自动化生产线提供技术支持。
1任务来源
由于某机匣零件材料硬度较大,且外型面比较复杂,精铣加工过程中还存在较大的提升空间,同时2018年技改将对某设备进行改善,增加在线测量设备和机内对刀设备,并对设备增加足够的刀柄以提高设备的整体加工能力,这样在硬件上已经满足了某机匣精铣无人值守的基本条件,通过在线测量、机内对开功能的开发应用,并对数控程序、加工方案进行优化、固化加工参数及加工刀具,可以有效地提高某机匣精铣的加工效率及零件加工质量,尽可能地减少现场操作者对零件加工状态的干预,保证现场零件加工的一致性,实现精铣高效加工。
2技术方案的制定及实施
机床综合应用开发,属于系统性性的研究,需要从技术和过程管理2个方面同时入手,通过技术实现加工的规范化、流程化以及数字化,通过管理,提供和保证技术实施所需要的条件,保证项目的顺利实施,即从工装定位管理、工装的装夹找正、刀具选择与配送管理、刀具的装、卸要求、刀具的测量、刀具寿命管理、加工流程方案、零件检验,机床的维护和保养、在线测量系统、机内对刀系统地运用及管理等内容,制定规范的加工流程,降低数控加工中的风险,充分发挥数控机床的设备功能,实现自动化加工,同时在刀具管理、设备维护以及改革现有制度,为加工流程提供可靠的硬件保证。技术的提升和硬件条件的保证,加上管理的完善,将提升机床的综合利用利用能力。
2.1零件需要人为干预的因素分析
零件需要人为干预的因素主要包括加工刀具的检测、加工刀具的刀长输入、零件加工过程中的尺寸测量、装配销钉加工过程中的拆卸以及零件加工后尺寸测量等。
2.2解决方案的制定
2.2.1自动对刀系统应用
BLUM激光刀具检测系统是一套精度极高的光学测量装置,可以在加工过程中监控加工中心的刀具状况并进行自动刀具测量。检测刀具的几何轮廓,能及早地侦测出调用错误及预设错误的刀具,同时也可以得知刀具是否已破损或磨损过量。这种操作方式可以有效地避免工件及后续刀具的损坏。
2.2.1.1测量与设定循环
测量操作前,要求预设刀具数据,精度为±5mm,测量后得到的数据被输入刀具表。测量速度、移动行程及退出动作均在每次测量动作中逐步地变小。该运行方式可实现更短的测量时间。测量模式–1,–2,–3中,刀具被直接快速定位到光线中(错误的刀具数据可能导致撞机)。测量模式0,1,2,3中,包括在一定范围内搜索并确定刀长的动作,长度超过预设值的刀具将被检出,不会有撞机的危险。
2.2.1.2应用优点应用优点
如下。1)刀具是在旋转状态下对刀,因此更接近加工状态,对刀精度更高。2)在刀具、刀柄与设备完成装配之后对刀,消除了一些装配误差。3)无须手动输入刀长信息,由系统自动输入,避免了手动刀长输入错误的情况。
需要注意的是,自动对刀精度与机床温度有关,在对刀前主轴应该自转几分钟预热后再加工,同时机床应该定期保养、维护。
2.2.2在线测量系统应用
数控设备加工在线检测系统主要包括数控机床自身、测头系统、计算机以及测量软件等。其中测头系统由触发式测头、测头信号接收器以及接口电路等组成,并与数控机床控制系统配套使用,实现测点的触发功能。
数控加工中心在线测量免去了工件的反复装夹、校正的过程,比离线检测减少了工件检测的时间,提高了检测效率。在成本方面,仅需安装在机检测测头和相应软件即可完成检测工作。由于加工与检测在同机上完成,检测反馈信息可以用于修改加工G代码,形成加工—检测—再加工的闭环系统,将大大提高尺寸的合格率。
3某后机匣零件整体加工方案
3.1精铣工序拆卸钉流程优化
由于对开机匣结构的特点,在精铣外型面工序对开安装边两侧存在螺钉、螺帽和定位销等工艺件,影响零件的加工,因此在零件整体加工过程中人为进行工艺件拆卸是不可避免的。
该种加工方案存在3个优点,首先人为干预的次数尽可能地减少,其次将人为干预提前,保证后续自动化加工程度,最终控制零件装配状态,保证后续加工表面接刀、尺寸测量等方面精度。
3.2对开安装边壁厚尺寸控制方案
对于对开机匣类零件,在精铣过程中对开安装边两侧壁厚尺寸与零件加工状态有关,一旦出现偏差,就会导致安装边中线两侧不对称导致零件尺寸超差,因此经常需要在加工过程中操作者手动测量,并调整控制加工程序,以保证安装边壁厚尺寸,而此壁厚尺寸很难通过在线测量手段在加工状态进行测量,通常只能通过游标卡尺手动比较测量。
3.2.1方案1
在工艺规程中增加铣顶部平面工序,使对开安装边中心线与机匣理论圆中心线重合,消除线切割工序、镗结合面所造成加工误差,为后续的半精车、精车工序提供找正基准,确保后续精加工工序机匣两半部的一致性和对称性,保证后续零件加工状态。
3.2.2方案2
在数控程序加工坐标系中增加G55坐标系,涉及对开安装边壁厚尺寸全部分开,以对开结合面线为基准进行加工,确保两半部结合面壁厚尺寸合格。
3.3某机匣外型面表面接刀控制方案
某机匣表面使用Φ20整体合金铣刀铣加工大面,横向加强筋转接R为R6.5,所以在清根时使用Φ20R6.5整体合金铣刀加工,由于材料硬度、刀具材料和机床精度等多方面的原因,导致在加工过程中两刀的接刀位置常常出现一条比较明显的接刀痕迹,此痕迹常需要手动调整刀长值进行补偿,影响后续零件无人值守加工表面精度。
试验了多个方法,包括调整加工顺序、走刀路线、加工参数、更换加工刀具品牌,该接刀痕一直存在,后来调整加工刀具,铣大面与清根保持一致都使用Φ20R6.5铣刀进行加工,确保清根刀具与铣大面刀具使用同一把刀,以控制表面接刀痕迹,优化后零件表面质量得到了有效控制,消除了表面接刀痕。
3.4某机匣精铣自动对刀验证
激光测量系统使用前必须进行校准,即必须精确确定触发点的机床坐标。校准时使用BLUM特制的标准刀。标准刀要事先通过热缩方式或弹簧筒夹装入刀柄,并测量得到长度、直径及高度,精确到0.001mm。校准循环对标准刀进行“测量”,确定激光光线上触发点的精确位置。测量的结果写入校准参数中。这些参数禁止被其他程序改写。在之后的刀具测量过程中,这些参数用于刀具在光线中的定位,并用于计算刀长和半径。
通过长期的跟踪和数据分析,机内对刀系统的稳定性是可靠的,由于不受外部因素影响,比机外对刀仪操作者手动测量数据的一致性更好。两者的测量数据的平均值差距较小。对于加工的准确性比较,可通过修正机内、外对刀系统标准刀数据进行调整,由于两系统误差差距在0.02mm左右,相对机匣零件的直径公差0.10mm,不会带来质量风险,可在运用中测量比较分析,对具体刀具进行补偿使用。
相关期刊推荐:《中国新技术新产品》(半月刊)创刊于1993年,是由国家科技部主管、中国民营科技促进会和科技部火炬高技术产业开发中心主办的指导性科技期刊。设有:总编推荐、本刊特稿、国家科技政策解读与科技计划、技术产品、产业观察、区域经济与自主创新、精品赏析、创新创业等栏目。
机内对刀系统是个精密的系统,为了保证机内对刀测量的结果准确性,稳定性,制定如下5点操作要求:1)每天机内对刀仪应用前需调用主轴预热程序预热5min,每天进行一次标准刀校准,保证系统测量准确性。同时检查机内对刀仪上激光发射/接收孔内是否有油泥,用直径为2mm的硬性塑料管将其清除。2)每次刀具装夹时,检查刀柄前端弹簧套是否损坏,刀柄后端拉钉是否拧紧,控制刀具摆动带来的测量误差。3)在测量前,主轴倍率一定放置在100%位置,防止出现报警,影响测量结果,进给倍率不能小于100%,避免影响测量速度。4)定期清除所有刀具刀柄上和主轴中的锈迹,在每周五进行检查,控制重复装夹误差,同时重点清理机内系统的标准刀刀柄,在机外对刀仪上检查其长度是否有变动。5)每周第一把刀在测量后用工作台测量基准和对刀块进行手动校对检查。
3.5某机匣精铣外型刀具选择
某机匣精铣外型刀具选择:应用于加工中心进行高速高效切削的数控刀具不仅要硬度、强度高、耐磨性、韧性好,同时还需要具有高的可靠性、切削稳定、质量一致、换刀次数少、寿命长、安装精度高、重复定位好,互换性好,良好的断屑、排屑性能,为了选择合适的刀具,在某机匣外型面工序加工中,在刀具寿命、成本、加工质量稳定方面,通过多年来对各种品牌刀具进行试验验证,选用金鹭、成量品牌的刀具进行加工。完善刀具在机床中的管理:1)规范机床的刀具命名,统一编程、仿真、机床各个系统之间的刀具命名规则,消除以前的孤岛模式,保证批准的程序可以直接使用,无须手动更改刀具名称。2)固化每种刀具在刀库中的位置,既可通过主轴将刀具放回刀库位置,也可以通过刀库管理器直接放回刀库,在机床刀具表中的刀具与刀库中刀具位置不会发生混乱。这也是将来生产线必须确定的工作。
3.6某机匣精铣在线测量验证
使用夹具作为在线测量的标准件,因此在夹具的装夹有跳动的要求,圆周跳动不大于0.03,端面跳动不大于0.01,使用夹具的止口位置作为Z方向的标准件测量,使用夹具的定位面位置作为Y方向的标准件测量。
3.7零件加工前试切测量
由于零件材料、刀具材料、机床加工精度、零件状态和冷却液浓度等多方面原因,在加工过程中我们加工零件的实际数值与理论数值会出现一定的偏差及让刀,因此需要对零件进行试切加工,并进行机床在线测量,将试切的偏差值进行补偿,确保后续尺寸加工合格。对纵向加强筋上部进行试切加工,并单边预留0.5mm余量,使用在线测量功能对零件加工尺寸进行测量。后机匣在加工过程中需要测量保证的是外型面直径尺寸以及横向加强筋的轴向尺寸。
3.8某机匣精铣在线测量UG编程
零件测量程序编制,由于三坐标测量程序测量点比较多,因此研究开发使用UG软件实现测量程序的编制,以下是测量程序的测量点位及测量轨迹,如图1所示。
根据SJAO系列设备特点及BLUM系统编程结构完成了SAJO系列BLUM系统在线测量UG后处理文件,根据测量轨迹完成测量程序的输出。
4结论
该项目以某机床为平台,某机匣零件为载体,全过程质量控制为研究主线,从刀具、虚拟制造技术(切削参数)、在线测量、机内对刀、机床的维护、工装的管理和加工流程等方面进行了系统性的开发及研究,建立了一套适合对开机匣零件数控加工的机床高效应用模式。某机匣零件加工过程除了零件装夹工作以外,机床加工零件所需的卸刀、装刀、主轴预热,机内对刀等所有动作都编制进流程程序,操作者只需要一步步按照流程程序运行过程中的信息提示,完成必要的操作,就能保证零件后续加工不间断的进行,并自动完成在线测量等工作,基本实现单机柔性加工单元进行的工作。整个流程操作者3h完成必要工作,后续16h无须职守,并自动完成在线测量等工作。该机床综合应用方案涉及的技术及管理方案符合工厂大部数控加工中心,有较大的推广前景,随着该机床使用技术的推广,成熟度提升,工厂的加工能力、管理水平,必然得到相应的提升,使机匣厂形成独立加工中心与柔性生产线配套良性循环发展的模式,全面提升工厂在科研、批产各方面的能力,逐步达到国际数控加工先进水平。——论文作者:陈亚莉1郑忆南2于浩2李娜2