数字孪生技术及其在石油化工行业的应用
发布时间:2021-03-09所属分类:计算机职称论文浏览:1次
摘 要: 摘要:数字孪生是一种可以完成信息世界与物理世界等价映射的新兴技术,其在传统石油化工行业的应用正在不断增加。本文阐述了数字孪生的内涵和关键技术,总结了近年来数字孪生技术在石油化工行业的应用进展,指出了其在石油化工领域遇到的挑战,探讨了发展趋
摘要:数字孪生是一种可以完成信息世界与物理世界等价映射的新兴技术,其在传统石油化工行业的应用正在不断增加。本文阐述了数字孪生的内涵和关键技术,总结了近年来数字孪生技术在石油化工行业的应用进展,指出了其在石油化工领域遇到的挑战,探讨了发展趋势。通过开展数字孪生在石油化工生产过程建模与参数优化、工艺参数设计与仿真、系统健康监测与远程维护等方面的应用研究,有效提高了石油化工领域的数字化、智能化程度。未来在标准体系构建、融合5G技术的数据采集与传输、智能信息处理算法等方面,需进一步开展研究。
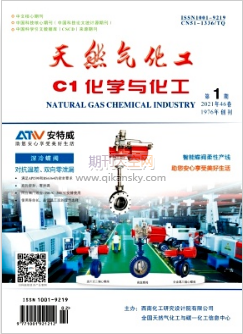
关键词:数字孪生;石油化工;关键技术;应用前景
近年来我国石油化工技术大幅提升、产业规模不断扩大,但目前国内市场仍有64.5%的石油依赖进口,其主要原因不仅中国是石油消费大国,同时石油化工技术也需进一步发展。技术创新不够是阻碍中国石油化工行业快速发展的主要原因,其直接导致石油化工产品生产时面临资源浪费、环境污染大、产品质量差、生产效率低等问题。与此同时,数字化成为了新经济条件下工业发展的新引擎,而数字孪生技术正好满足了让物理与信息世界相互融合、实现数字化转型的智能制造与流程工业的要求,因而受到了石油化工行业的广泛关注。
数字孪生在石化行业的应用,为产品质量差、生产效率低、产品难以销售等问题提供了一种切实可行的解决方案,越来越多的石油化工企业选择用数字孪生构建生产模型以帮助自身发展。然而,目前在石油化工领域,数字孪生技术的应用仍处于初级阶段,大部分研究仍停留在理论阶段,缺乏实际应用,因此要实现数字孪生在石油化工行业的真正落地,还需要科研人员与企业进一步紧密合作,开展更深层次的研究。
1数字孪生技术概述
1.1数字孪生内涵
1969年,NASA在阿波罗项目中为了确保“在轨零故障”,利用在轨装配技术,构建能够反映正在工作的航天器状态的孪生体,以通过大量模拟测试降低成本,这是数字孪生发展的起源[1]。格里夫斯(Grieves)教授于2003年提出了“PLM(产品全生命周期)管理”和“用虚拟数字等价物理产品”的概念,并给出了详细定义,这意味着数字孪生的正式出现。格里夫斯教授由此获得了“数字孪生之父”的称号[2]。2003鄄2005年期间,数字孪生技术被称为“镜像空间模型”,之后又被称为“信息镜像模型”[3]。直到2011年,数字孪生这个名称才正式确定,定义为“一种能够将虚拟产品及其连接实体化的三维模型”,其功能是将物理产品映射到虚拟信息空间,而且实时监测产品的全生命周期,使产品维运过程得到优化[2]。随着飞行器技术要求的提高,研究人员开始将数字孪生与飞行器设计相结合,设计过程中,数字孪生体被描述为一种仿真模型,它能够通过物理模型和各种数据反映与之相对应物理实体的各种属性[4]。同时,美国空军将数字孪生的功能定义为“能够在虚拟信息空间反映物理实体的功能、实时状态和演变趋势”[5]。面向通用民用产品的数字孪生体于2015年正式出现,并由此开始在民用基础工业获得了应用。2017年,面向车间的数字孪生体(数字车间)的出现,不仅使制造车间开始步入数字化转型阶段,还为建造制造车间CPS提供了相关理论基础。
1.2数字孪生的关键技术
数字孪生的关键技术主要有:多领域多尺度融合建模、数据采集和传输技术、VR呈现、高性能计算、数据驱动与物理模型融合的状态评估、全寿命周期数据管理等方面[5鄄8]。
(1)多领域多尺度融合建模
多领域建模是指在特定领域建模的基础上,通过融合集成数据将来自不同领域的模型组合成为一个包含不同属性的综合模型;多尺度模型是对单尺度模型的多维度扩展,调节物理参数来连接不同时间下的同一个模型并且分析不同时间模型的工作状态,以获得更高的模型精度。
(2)数据采集和传输
数据高效采集和传输是数字孪生技术实现的基础,同时先进可靠的传输网络使采集到的数据能够快速、准确地传输到数据中心,为数字孪生技术实时应用提供保障,以保证数字孪生系统的实时性。
(3)VR呈现
VR技术不仅复现了目标系统的状态,还能将采集到的数据信息通过虚拟映射到创造的数字孪生系统中,保证了人机互动的实时连续性。VR技术通过数字孪生系统让使用者快速地学习和了解目标系统的各种信息,帮助使用者激发改进系统的灵感,有利于人们实时监控、指导复杂装备的制造、运行和维修。
(4)高性能计算
由于需要实时映射,数字孪生系统应当具有强大的计算能力。考虑到硬件技术发展水平,目前主要通过将基于分布式计算云平台作为基础,辅以融合高性能嵌入式计算系统和异构加速计算体系,并通过优化数据分布层次、检索方法和存储形式,以提髙运算性能。
(5)全寿命周期数据管理
复杂系统的全寿命周期数据存储和管理是数字孪生系统另一关键技术,其通过云服务器分布式管理、高速读取并且备份冗余数据,为数据解析算法的发展提供大量可靠的数据,对维持整个数字孪生系统的运行起着重要作用。
(6)其他关键技术
人工智能的发展为数字孪生技术提供了前进动力,在不同的数字孪生应用场景中,利用量化分析、无样本或小样本的增强学习能够优化数据生成、建模和数据分析。此外,半物理仿真、验证和评估法等方法在构建数字孪生平台过程中也非常重要。这些技术与数字孪生的结合,能够极大提高数字孪生系统的性能,推动数字孪生技术的进一步发展。
2数字孪生技术在石油化工行业的应用
2.1数字孪生技术在石油化工行业的研究及应用现状
利用数字孪生技术设计出能够虚拟映射实体工厂的数字模型,是实现石油化工领域数字化转型与发展的关键路径。目前,国内外各类研究机构和大型企业积极布局,不断突破数字孪生技术的关键技术。陶飞等[9]提出了一种数字孪生车间概念及实现模式,包括车间孪生数据、物理车间、虚拟车间、车间服务等,将实时车间数据反馈到虚拟空间进行分析然后用算法进行优化,从而有效地解决了车间里管理制度差和决策效率低等问题,图1为数字孪生车间模型示意图。Zhang等[10]利用CPS,提出了一种资源加工服务状态的实时感知和自主决策智能建模方法,以解决工厂生产时遇到的资源配置与自适应协同控制的问题。达索公司为满足复杂产品用户的交互需求,建设了3D交互平台;设计者利用该平台可以持续收集用户的反馈信息,然后利用这些信息优化产品的虚拟模型,并最终改进产品实物的性能[11]。
对于石油化工行业,数字孪生技术研究及应用主要集中在生产全流程和产后维护上,即油气勘探开发、钻井过程、石油工程装备全生命周期等[12鄄16]。
(1)油气勘探开发综合系统数字化
利用物联网、云计算、大数据、人工智能等技术,深入挖掘现有的油田勘探数据资源,寻找油气勘探开发数字孪生实现方法,将油气勘探开发的物理空间映射到虚拟数字空间,并与数字孪生系统进行融合。利用这种方式将改进现有汽油勘探模式与技术,降低石油勘探开发成本。基于这种理论,中油瑞飞打造了一种所谓“石油大脑”,该系统融合虚拟现实,在数字虚拟模型上实现了油气现场勘探开发与状态管理、员工培训与现场可视化作业、场外专家在线指导等功能。目前,“石油大脑”被应用在西南油气田、大庆、渤海等地的开采和钻探过程中。
(2)石油工程装备全生命周期数字化
在石油工程装备管理平台的基础上开展装备全数字化技术研究,构建装备工业物联网,探索设计、生产、操纵、经营、维护等生命周期数据之间的联系,在数字孪生系统中把控产品质量,在装备现场验证数据正确性,提升装备机能并改进其生产工艺,无需亲临现场,通过数字孪生系统远程监控各类数据,全方位数字化石油工程装备,实现智能石油工程建设与智慧化发展的景愿。2017年,新疆油田就已经开始了石油工程装备全生命周期数字化的研究;2019年7月,新疆油田公司地面建设工程“全生命周期”数字化管理平台基本建成,克拉玛依气田、玛河气田天然气增压及深冷提效两项试点工程数字化交付整体进度分别达到80%、48%。随着这种基于数字孪生技术的石油工程装备管理平台示范应用进一步扩大与成熟,全国其他油田也会逐步将其投入推广使用,带来数字孪生技术在石油工程装备管理方面的更大进步。
(3)钻井过程数字孪生
在半潜式钻井平台的基础上开展数字化研究,通过创建物理信息系统来监测数据驱动信息空间中构建的设备运行状态,实现钻井平台关键设备变化情况的模拟和预测,达到实现钻井平台与虚拟空间模型相互映射、相互指导的作用。目前,美国通用电气公司依托工业互联网,与知名钻井承包商诺贝尔公司(NobelCorporation)、美国船级社(ABS)、马士基钻井公司(MaerskDrilling)合作,开始了数字钻井船和数字孪生体的试点工作。预计不久后,钻井平台的数字孪生模型就能正式建成。未来,钻井过程数字孪生技术有望发展到钻井过程全生命周期中,基本过程大致概括为:结合各种工程技术对地面及井下数据进行检测,选择出最优施工方案,预测施工过程中可能出现的异常并给出处理方案等。
(4)石油管道数字孪生建设
石油管道运营商可以通过在线监测,获得大量管道运行数据,但如何利用这些数据、实现数据可视化一直是石油管理领域的难点。数字孪生利用虚拟现实技术,获得3D石油管道数据图像。用户通过对石油管道虚拟图像进行处理,利用全息透视眼镜,便可清晰观测管道内情况。同时,将管道附近反映地质变化状况的重点区域进行热图成像,用户利用该图像便能更好地发现小凹痕、裂缝、腐蚀区域等地质变化状态以及管道应变等潜在危险。该技术被评为2018年国际石油十大科技进展之一[17],目前在加拿大Enbridge公司得到了成功应用。实践表明采用该技术节省了管道数据分析和处理时间,提高了管道完整性评估的快速准确性,从而证实了管道监控的有效性。
(5)石化行业数字工厂应用平台
传统的石化工厂信息系统一般是基于传统业务驱动型的,包括EPR系统(即企业资源计划系统)、MES系统(即制造执行系统)、维修管理系统、安全环保系统等。新型的石化工厂在传统的业务驱动型信息系统基础上,还包括大数据分析、数据挖掘、先进控制、在线实时优化、工业云平台等,其主要通过数字工厂与管理系统的集成、数字工厂与生产过程监控的集成、数字工厂与设备管理系统的集成、集成数字工厂的工艺培训管理集成等体现[1]。
相关期刊推荐:《天然气化工(C1化学与化工)》本刊主要报道天然气和一碳化工、石油化工及精细有机化工领域的科技新成果、新工艺及技术进展、动态信息等。包括合成气的净化、分离技术,合成气生产技术,天然气和合成气的化工利用技术(合成甲醇和甲醛,合成氨,合成氢氰酸、乙炔、甲烷氯化物和二硫化碳,制氢和氢气的利用,合成烯烃,合成燃料(油和二甲醚等),羰基合成醇、碳酸二甲酯、醋酸及其他大宗或精细化工产品,加氢甲酰化合成化工产品,二氧化碳化工利用技术等),天然气和一碳化工衍生产品的深加工利用技术,天然气加工及石油炼制与化工副产的低碳烷烃(C1~C5)的化工利用技术,同时也报道本领域国内外的最新动态信息和一些其他领域的化工新技术。
虽然石油化工行业数字孪生研究已经取得了一些成果,但是就目前的实际应用情况而言,其应用还处在刚刚起步阶段。国内数字孪生技术主要在一些大型企业如中石油、中石化点应用[18],中小企业因缺乏技术指导和相关设备,很少有应用案例。同时,国家还没有制定相关的数字化标准,管理上也存在一些漏洞。因此,数字孪生技术在石油化工的大范围推广应用还需进一步深入研究。
2.2数字孪生技术在石油化工行业的开发应用
目前,数字孪生在石油化工领域还处于初步阶段,离大规模应用还有很大的差距,但是研究重点已经基本确定,主要集中在如下四个方面[19]:建设目标、系统总体架构、系统主要功能、应用场景探索。
(1)建设目标
若要完成石油化工领域全面智能化流程行业的任务,就必须研制出与之相对应的数字孪生系统框架。通过改进信息系统与物理系统的融合方法,优化多时空、多尺度模型的参数求解性能,并提升石油化工关键工艺指标的预测能力。同时,进一步完善关键应用场景中的石油化工系统故障诊断、工艺参数优化等的数字孪生解决方案,使其更加有效、实用。
(2)系统整体结构
首先,在数字孪生的基础上构建一个模拟的石油化工物理实体状态的虚拟模型,再利用各种传感器等基础设施,采集石油化工领域生产流程可能涉及到的所有数据,实现信息和物理的融合,最终将石油化工的物理实体完全映射到虚拟实体上,同时利用各种优化算法改进与优化模型参数。
(3)系统主要功能
①在石油化工行业中引入数字孪生技术的主要目的是模拟、分析、优化、监控与预测设备和系统运行过程等。通过模拟设备的运转过程,得到各种性能参数,然后将这些参数加入模型进行分析,以预测关键生产装置质量和和关键控制指标,最后对设备和系统过程进行优化调整。
②融合全生命周期数据,即通过数字孪生技术,以建立的虚拟模型作为载体,收集分析石油化工系统全生命周期的数据,将系统属性状态、运行情况、关键工艺参数与系统运行情况等映射到虚拟模型中,最后虚拟模型根据分析处理后的数据调整所有生产过程,促进石油化工信息共享,实现全流程协同工作。
(4)应用场景探索
①优化组成原料。石油生产时,生产条件可能不是固定的,其涉及各种模型且产生过程中操作成本均不一样,因此需要对生产原料等进行优化。
②工艺参数设计与仿真。采用流程模拟软件构建机理模型,并利用各种优化算法对导入的现场数据进行处理以校正模型,以达到提升系统全流程模型准确性的目的。
③过程建模与参数优化。构造目标函数、开发出合适的优化器,然后根据目标函数和约束条件求解模型最优值,并给出所需要的操作条件,以达到能够在最优操作条件下实时指导生产过程并且优化控制目标的目的。
④设备故障诊断与远程运维。为保证设备能够安全可靠地运行,必须利用各种算法和模型,例如设备故障诊断模型、维修策略模型以及参数预测算法等,对设备运行状况和生产过程实施在线监控与健康评估,并自动给出诊断报告、提供解决方案。
2.3数字孪生技术在石油化工行业的前景分析
为了在扩大生产规模的同时保证产品质量并且提供个性化服务,越来越多的石油化工企业通过构建石油化工产品的数字孪生体,提高产品质量、降低生产成本。目前,数字孪生技术在石油化工行业的应用已经取得初步成效,其发展趋势包括以下三个方面。
(1)融合5G技术的数据采集与传输
数据高效采集和传输是数字孪生技术实现的基础。石油化工工厂复杂、需要采集的信息节点多、自动化程度要求高,这就要求在实施数字孪生技术时,必须保证高效、准确的数据采集与传输。“5G+产业互联网”可以将石油化工工厂的信息流、指令流、操作流等一体化,完成各环节的在线远程控制,实现石油化工系统与设备的数字孪生[20]。更进一步发展,“5G+产业互联网”能够采集和获取全社会生产资源、生产过程、生产能力信息,实现大规模海量协同的长尾效应,促进石油化工工厂生产行为习惯和方式的逐级优化、高速迭代,获得最大效益。
另一方面,随着数字孪生发展,网络安全问题显得尤为重要。由于数字孪生技术的引入与加速融合,石油化工系统由原来的封闭系统向开放系统转变。为了保持高效率和实现资源控制,要求网络连接流程尽可能简化,以便高效顺畅,但系统的网络安全风险将完全暴露。若“5G+石油化工互联网”受到攻击,严重时将有可能直接摧毁石油化工企业的生产能力,造成巨大损失。
因此,融合5G通信技术,并构建数字孪生网络安全保障体系,解决数字孪生海量数据采集与传输问题,将是石油化工领域数字孪生技术的发展方向之一。
(2)数字孪生智能信息处理方法
石油化工系统复杂,数据源多、具有时变性,系统模型多样、耦合困难,系统计算复杂、模型求解难度大,传统的信息处理方法越来越力不从心,给数字孪生在石油化工领域的应用带来了极大挑战。云计算与云存储、大数据、区块链、人工智能等为数字孪生的处理、系统建模提供了有效手段。如何利用这些智能方法,更好、更有效地完成数字孪生信息处理,是数字孪生在石油化工领域的发展方向之一。
(3)数字孪生标准体系构建
目前,国内石油化工行业的数字孪生标准体系尚未构建,严重阻碍了其进一步发展和应用推广[21]。主要体现在:①缺乏石油化工行业数字孪生相关术语、系统架构等标准化参考,不同企业和用户对数字孪生的理解与认识存在差异,在人员交流、技术集成、工程协作过程中存在困难;②缺乏石油化工数字孪生相关模型、数据、服务等标准化参考,导致模型间、数据间、系统间难以集成,兼容性差;③数字孪生在石油化工行业中实施时,由于缺乏适用准则、实施要求等标准的参考,给用户和企业带来了极大困惑,增加了实施成本。因此数字孪生的研究人员需要在开展理论研究的同时,加强与应用企业和石油化工领域相关标准化组织的协同合作,共同构建一套石油化工行业的数字孪生标准体系架构。
3结作
为目前数字化领域中最有应用前景的技术之一,数字孪生发展迅速,在多个领域应用方兴未艾。石油化工作为国家重要的战略型行业,利用数字孪生技术能够实现行业技术升级,极大提高行业经济效益和社会效益。目前,通过开展数字孪生在石油化工生产过程建模与参数优化、工艺参数设计与仿真、系统健康监测与远程维护等方面的应用研究,有效提高了石油化工领域的数字化、智能化程度,取得了初步成效。然而,数字孪生技术在石油化工行业的真正落地和大范围推广应用存在一些挑战。未来几年,石油化工领域的数字孪生将在标准体系构建、融合5G技术的数据采集与传输、智能信息处理算法方面等开展进一步的研究工作。——论文作者:陈岳飞1,2,肖珍芳3,方向1