电弧喷涂耐海水腐蚀金属涂层的研究进展
发布时间:2022-03-16所属分类:工程师职称论文浏览:1次
摘 要: 电弧喷涂金属涂层作为钢结构表面防护的一种重要措施,经过几十年的发展,已成为成熟的表面工程技术和产业。同时,随着新的喷涂工艺、设备和材料的不断研发,电弧喷涂金属涂层应用领域日益广泛。与此同时,使用电弧喷涂技术进行防腐的缺点也日益突出,尤其是喷涂过程中
电弧喷涂金属涂层作为钢结构表面防护的一种重要措施,经过几十年的发展,已成为成熟的表面工程技术和产业。同时,随着新的喷涂工艺、设备和材料的不断研发,电弧喷涂金属涂层应用领域日益广泛。与此同时,使用电弧喷涂技术进行防腐的缺点也日益突出,尤其是喷涂过程中存在有害物质排放等问题,严重制约了其发展。电弧喷涂制备的涂层孔隙率低、微观组织致密、结合强度高且经济性好。相比于其他传统防腐技术,电弧喷涂金属涂层应用于钢结构的表面防护具有如下优势: ( 1) 电弧喷涂沉积效率高、操作容易,便于现场施工; ( 2) 涂层在海洋苛刻腐蚀环境中服役时间长。
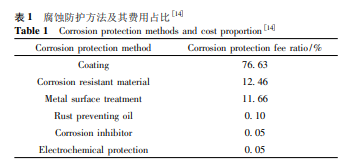
然而,电弧喷涂耐海水腐蚀金属涂层的服役环境介质不同,对涂层的耐蚀性能提出了更高的要求。因此,近几十年来除研究电弧喷涂工艺参数外,科研工作者们着力研发多功能、高性能的喷涂材料,并取得了丰硕成果,同时充分利用电弧喷涂技术的优势可显著提高涂层的性能。目前电弧喷涂金属涂层材料正朝着复合化、新型化方向发展。
目前,用于钢结构表面防护且已取得广泛应用的喷涂材料有锌/铝及其合金、镍基合金、铁基合金和铜基合金等。其中锌、铝及其合金是使用最早且最广泛的喷涂材料; 镍基合金可通过加入铬、钼等抗点蚀、缝隙腐蚀的合金元素,提高材料的耐蚀性能; 铁基合金中添加少量 Mo 等元素,能有效抑制晶界腐蚀发生; 铜基合金中加入 1%的锡,能抑制合金脱锌过程并提高其力学性能。近几年的研究重点为多种合金材料复合及新型合金材料的使用,以电弧喷涂技术为手段制备耐腐蚀涂层,可实现涂层功能和性能的双提升。
本文以分析钢结构在近海岸海洋环境各区域带的腐蚀规律为基础,比较了目前用于钢结构表面腐蚀防护的方法及其优缺点,阐述了电弧喷涂涂层的研究现状和防腐机理。从电弧喷涂耐海水腐蚀涂层的微观组织结构、涂层性能及防腐机理等方面,分析了电弧喷涂金属涂层防腐面临的问题并展望了其前景,以期为工业领域钢结构表面的长效防护提供参考。
关键词 电弧喷涂 海水腐蚀 腐蚀规律 腐蚀机理 腐蚀防护
0 引言
随着世界工业的快速发展,油气等自然资源的需求量也迅猛增长[1]。虽然全球的油气资源总量丰富,但由于陆地地形复杂及开采难度大等原因,可供开采的资源十分有限,已不能满足工业生产的实际需求; 而占地球总面积 71%的海洋区域是拥有丰富的矿物、生物和油气等资源的宝库,且开采潜力巨大,因此油气资源开采要向海洋尤其是深海领域延伸[2-3]。
深海油气资源的开采面临一系列问题,其中海洋环境的 “腐蚀”是当前面临的最大挑战。海水盐度为 34%,是一种强电解质弱碱性溶液,含有大量的氯离子。氯离子由于半径小、活性大,容易破坏海洋钢结构表面的钝化膜,使得钢结构表面发生腐蚀[4-5]。海洋油气资源开采平台在整个使用寿命周期内,不仅受到海水的腐蚀作用,同时波浪、潮汐和洋流等又会对钢结构产生交变应力和冲击作用[6],且海洋环境中的微生物、附着生物以及它们的新陈代谢产物等都会加速钢结构的腐蚀[7]。海水腐蚀是导致海洋基础设施发生腐蚀破坏的主要原因,严重时会引发油气管道泄漏,破坏海洋生态系统[8]。因此钢结构表面需要进行长效防护处理,以抑制海洋腐蚀的发生,确保深海领域资源开采成套设备的长周期安全稳定运行[9-10]。
目前用于钢结构表面防护的方法主要有: ( 1) 表面涂装法,如在钢结构表面涂刷防腐涂料[11]; ( 2) 表面处理法,如通过电弧喷涂技术在钢结构表面制备涂层作为保护层,由于涂层的屏蔽作用,将基体表面与腐蚀性介质隔离,抑制腐蚀发生[12]; ( 3) 采用缓蚀剂保护、电化学保护[13]。表 1 为各种腐蚀防护方法及其费用占比[14]。钢结构表面涂刷防腐涂料不能满足深海开采平台设计寿命的使用要求; 缓蚀剂保护对材料-环境体系有较高要求,使用范围有限; 而电弧喷涂技术制备防腐涂层作为保护层[15],是钢结构表面长效防护中效果明显且操作简单的防腐措施。
1 钢结构的腐蚀与防护
1. 1 钢结构腐蚀
钢结构在海洋环境中的腐蚀行为与其服役的环境相关。为了更好地研究钢结构在不同海洋环境下的腐蚀规律,从而能够采取有针对性的措施进行防腐,这就需要对不同海洋环境的腐蚀规律开展大量研究。在海洋环境中,可以将钢结构的腐蚀区域划分为海洋大气区、浪花飞溅区、海水潮差区、海水全浸区以及海底泥土区[16-17]。由于各个区域带的工况不同,钢结构在不同区域带的腐蚀速率存在明显差别。图 1 为钢结构在不同海洋区域带的腐蚀示意图[18]。大量实海试验结果表明,钢结构在海洋大气区中的平均腐蚀速度为 0. 03 ~ 0. 08 mm /a,浪花飞溅区为 0. 3 ~ 0. 5 mm /a。同一种钢质材料在浪花飞溅区的腐蚀速度要比海水全浸区高出 3 ~ 10 倍,因此浪花飞溅区是海洋环境中腐蚀最严重的区域带[19-20]。这主要是由于浪花飞溅到钢结构表面,使其表面长期处于干湿交替的状态,且在供氧充足、盐分及氯离子不断浓缩的情况下,加之光照、海风和雨水等的相互作用,使得浪花飞溅区的腐蚀最为严重[21]。
钢结构一般要求寿命至少 20 ~ 30 年,目前钢结构表面采用重防腐涂料防护在浪花飞溅区只能正常工作 3 ~ 5 年左右[22],而电弧喷涂复合涂层在海洋环境中服役寿命为 30 ~ 50 年,因此电弧喷涂是一种经济有效且施工简单的长效防腐方法[23]。
1. 2 电弧喷涂防腐
腐蚀是钢结构最常见的表面破坏方式之一,因此大多数钢结构从设计时就加入必要的防腐工序对其进行保护,避免因腐蚀而造成经济损失。电弧喷涂作为钢结构表面防腐的一种重要方法,其防腐原理为物理隔离和电化学保护。电弧喷涂涂层的组织结构致密,能够在钢结构表面形成具有一定结合强度的保护层,使基体与腐蚀性介质隔离[24]。由于制备涂层存在孔隙等表面缺陷,腐蚀性介质可由孔隙等渗透进入基体表面而发生腐蚀[25]。因此电弧喷涂制备涂层的孔隙率大小是影响涂层耐蚀性能的重要因素,采用封孔处理可以降低所制备的涂层的孔隙率,抑制腐蚀性介质的渗透,提高涂层在苛刻腐蚀环境下的耐蚀性能[26-27]。电弧喷涂制备的镍基合金、铁基合金涂层等,其本身具备良好的耐蚀性能,进行封孔处理后,在海洋环境中的耐腐蚀性得以显著提高[28]。李红英等[29]研究发现,由于环氧树脂填充孔隙等表面缺陷,使得电弧喷涂 Zn 涂层在 3. 5% NaCl 溶液中表现出较好的耐腐蚀性能。
常用于钢结构表面防腐的喷涂材料是相对活泼的金属,如锌( Zn) 、铝( Al) 及其合金等。锌铝合金涂层在海洋环境中使用时,涂层中的 Zn 首先被腐蚀,形成不易溶于水的 ZnO 等腐蚀产物堆积在涂层表面[30-31]。一方面防止涂层中的金属元素继续被氧化腐蚀,另一方面 ZnO 等腐蚀产物堆积在涂层表面的孔隙等表面缺陷上,切断腐蚀性介质渗透进入基体表面的通道; 而合金中的铝元素与氧的亲和力大,在供氧充足时涂层表面形成组织致密且稳定的氧化膜,依靠氧化膜的屏蔽作用实现防腐效果[32]。对于锌镍、铝镁等阳极型喷涂材料,在强电解质环境下,其电极电位要比金属基体负。根据电化学腐蚀理论,即使制备的涂层有孔隙等表面缺陷,阳极型材料在腐蚀过程中充当阳极,与作为阴极的金属基体形成电流回路,阳极型喷涂材料首先被腐蚀消耗,能够为钢结构提供阴极保护[33-34]。
2 电弧喷涂金属材料
随着海洋工程应用对服役寿命和电弧喷涂涂层性能要求的不断提高,各种性能优异的金属材料被相继研发出来。目前已有应用的金属材料有铝/锌及其合金、镍基合金、铁基合金和铜基合金等。
2. 1 锌、铝及其合金
锌、铝及其合金是目前使用最广泛的电弧喷涂防腐材料。锌铝合金同时具备 Zn 的电化学活性高和 Al 的化学稳定性好的特性,已广泛应用于船舶和钢结构等领域的长效防护。电弧喷涂用锌铝合金材料主要是 Al 质量分数为 5%~ 25%的 Zn-Al 合金,还可通过高速电弧喷涂技术制备 Al 质量分数更高的锌铝伪合金涂层[35]。目前使用最多的是 Zn-15% Al 合金涂层,该涂层的微观组织结构主要是由富 Zn 相和富 Al 相构成[36]。
锌、铝及其合金材料对机械损伤和点蚀特别敏感,因而其可靠性变差,不能保证钢结构在使用周期内正常运转。针对锌、铝及其合金涂层防腐存在的问题,研究发现在锌、铝及其合金材料中加入适量的镁、硅和稀土( RE) 等元素可以显著提高涂层的耐腐蚀性能[37-38]。卢飞等[39]研究高速电弧喷涂 Zn-Al-Mg-RE 涂层在 3. 5% NaCl 溶液中的电化学腐蚀行为,结果表明,涂层具备优异的电化学保护和屏蔽特性,且腐蚀产物可以细化涂层表面的微观组织结构,使其耐腐蚀性能显著提高。蒋穹等[40]通过研究电弧喷涂 Al-Zn-Si-RE 合金涂层在 3. 5% NaCl 溶液中的腐蚀行为,发现合金中的 Si 和氧的亲和力较强,生成的 Si 薄膜能够在涂层内部反应生成硅酸盐物质,降低涂层中的氧化物含量[41-42]; 合金中加入稀土( RE) 元素可以改善涂层的微观组织结构,使得涂层结构更致密、孔隙率降低、耐蚀性更好。图 2 为涂层腐蚀试验后 Al-Zn-SiRE 涂层的横截面[40],腐蚀产物堆积在涂层表面,不仅在涂层表面形成保护层,而且填充孔隙等表面缺陷,提高其耐腐蚀性能。随着腐蚀试验时间的延长,保护层逐渐变薄,直至丧失屏蔽作用。但稀土( RE) 元素在涂层中的最佳质量比有待深入研究。研究者们制备了一系列金属基涂层,如 Zn-Al-Mg-Si[43]、Al-Ti-Si-RE[44]等,并通过实海挂片试验证实其耐腐蚀性能良好。
2. 2 镍基合金
镍基合金是一种重要的耐海水腐蚀材料[45]。镍基合金中含有抗点蚀、缝隙腐蚀的合金元素,如铜、铬、钼等[46]。镍对铜、铬和钼等元素的固溶度较高,能够形成固溶体合金,既保留了镍的电化学特性,又具备其他金属元素的耐腐蚀性能。目前电弧喷涂用镍基合金材料主要有镍铜合金[47]、镍铬合金[48]、镍钼合金[49]和镍铬钼合金[50]等。镍铜合金中主要含镍、铜和铁等元素,称为 Monel 合金,在苛刻腐蚀环境中表现出良好的耐腐蚀性。Bagherzadeh 等[51]研究了 Monel 合金在 5% HCl 溶液中的腐蚀行为,图 3 为 Monel 合金在 5% HCl 溶液中浸泡不同时间后测得的电化学阻抗谱的奈奎斯特图和伯德图,可以看出,随着浸泡时间的延长,试样电荷传递电阻增大,表明合金中的 Cu 元素发生了晶界溶解腐蚀,腐蚀产物在合金表面堆积形成保护层,提高了合金的耐蚀性。镍铬合金称为 Inconel 合金,合金中含有 15%~ 22%的 Cr,使合金在氧化条件下具备耐腐蚀性能及在高温环境中具备抗氧化能力[52]。钼对镍基合金的强化作用比铬好,目前常用的镍钼合金中钼元素含量为 26%~ 30%,抑制了镍基合金涂层表面发生局部腐蚀。孟新静等[53]研究了钼元素对涂层耐腐蚀性能的影响,在低碳钢基体上制备了 Ni-Cu-Mo 涂层,并对其进行电化学腐蚀实验,结果表明,钼元素提高了涂层的耐腐蚀性能,同时细化涂层表面微观结构。大量试验结果表明,在镍基合金中同时加入 16%~ 22%铬及 9%~ 18%钼等元素,可以提高涂层的抗点蚀和耐缝隙腐蚀能力,使得镍基合金涂层在海洋环境等苛刻腐蚀环境中表现出良好的耐蚀性能,为解决钢结构的长效防腐问题提供了可能[54]。由于镍基合金材料种类众多,影响其耐蚀性能的因素各异,制备镍基合金涂层进行防腐时,应研究不同热处理工艺对其耐腐蚀性能的影响,并注意腐蚀介质、服役条件与材料选取的匹配。
2. 3 铁基合金
在海洋环境中,不锈钢材料是一种具有优异防护性能的预合金型涂层材料[55]。目前喷涂用不锈钢材料主要有铁素体不锈钢[56]、奥氏体不锈钢[57]以及马氏体不锈钢[58]等。随着高速电弧喷涂设备的出现,喷涂不锈钢涂层的综合性能不断提高[59]。为了改善铁素体不锈钢材料晶界腐蚀敏感等的不足,研究者们在原铁素体不锈钢材料的基础上研发出抗氧化和抗应力腐蚀性能更优的超级铁素体不锈钢丝材,通过高速电弧喷涂涂层解决钢结构的长效防护问题[60-61]。奥氏体不锈钢材料具备良好的耐腐蚀性,但奥氏体不锈钢涂层在腐蚀过程中作为阴极,一旦涂层有缺陷,基体就会加快腐蚀,因此利用奥氏体不锈钢涂层对钢结构进行防护时,需要对涂层进行封孔处理[62-63]。Tajiri 等[64]在低碳钢表面制备奥氏体不锈钢涂层,封孔处理后进行长达 500 h 的盐雾试验,结果表明,未封孔涂层由于孔隙等缺陷存在,基体发生腐蚀; 而封孔涂层作为阴极腐蚀消耗,基体受到保护。为了改善该涂层的缺陷,在奥氏体不锈钢材料中加入少量 Mo、Cr、Ti、Nb 等元素,能够有效提高奥氏体不锈钢的耐腐蚀性能并抑制晶界腐蚀发生[65-66]。Pardo 等[67]研究 Mo 和 Mn 等元素的加入对奥氏体不锈钢耐点蚀性能的影响,图 4 为不同含量的 Mo 和 Mn 对奥氏体不锈钢腐蚀速率的影响,结果表明,Mo 含量越高、 Mn 含量越低,其耐腐蚀性能越好。马氏体不锈钢材料主要用于中等腐蚀环境下服役的钢结构的表面强化,尤其适用于轴类零部件表面的防护[68]。为了提高耐点蚀和应力腐蚀性能,研发出性能更优异的奥氏体-铁素体双相不锈钢材料,材料中铁素体相和奥氏体相各占一半,同时具备奥氏体不锈钢和铁素体不锈钢的优点,主要用于解决中性氯化物环境下的局部腐蚀问题[69-70]。
本文来源于:《材料导报》杂志是综述性材料科技刊物,反映材料科技发展动态和国家宏观政策,跟踪材料世界发展前沿和方向,评述材料研究进展,及新材料产业化进程;探讨传统材料产业改造中的问题;跟踪WTO对中国材料产业的影响;展示国家相关材料计划实施及研究开发新成果,促进高新技术材料的发展及产业化,为我国材料科技起引导作用。
为了充分发挥铁基合金材料在海洋腐蚀环境中的耐腐蚀性能,找出其与其他合金元素的最佳质量配比,研究人员应将铁基合金材料的生产与现有冶炼技术相结合,拓展铁基合金材料的使用范围。同时,在保证原有耐蚀性能不变的条件下,通过改变合金中各元素比例,确定最佳的质量比,这将是今后的研究重点。
2. 4 铜基合金
铜基合金在海水等腐蚀环境中表现出良好的耐蚀性能,且腐蚀后,合金的强度、延伸率等力学性能均无明显变化[71]。
在钢结构表面利用高速电弧喷涂技术制备的铜基合金涂层组织致密、结合强度高、耐磨抗冲蚀性能优异; 同时可消除基体中的残余应力,加固构件表面钝化膜,提高了钢结构的服役寿命[72-73]。另外,在铜基合金中加入 1%的锡,能抑制合金的脱锌过程并提高合金的力学性能和耐蚀能力[74]。刘基凯等[75]研究电弧喷涂铜基合金涂层的耐蚀性能,冲蚀试验表明,由于涂层内部形成的层状结构氧化铝硬质相硬度高,抵消了磨粒的切削力,提高了涂层的耐蚀性能。同时,电弧喷涂参数直接影响着铜基合金涂层的耐腐蚀性能,因此正确的喷涂参数是获得综合性能优异的涂层的关键。Henkel 等[76]研究电弧喷涂送丝速度对涂层的残余应力状态分布及耐蚀性能的影响,通过改变送丝速度来影响热传递,从而产生不同应力状态分布,结果表明,最高送丝速度制备的涂层的表面拉伸残余应力最大,且抗冲蚀性能最弱。
除了以上目前普遍采用的电弧喷涂防腐材料,研究者们也研发出其他新型的喷涂金属材料,如锆基合金[77]、钼基合金[78]等。喷涂材料的发展拓展了电弧喷涂技术在腐蚀防护领域的应用,极大地提升了海洋环境钢结构的使用寿命。
3 结语与展望
电弧喷涂防腐金属材料正朝着性能日益优异、功能多元化的复合材料[79]、纳米材料[80]、新型合金材料[81] 等方向发展。目前,电弧喷涂长效防腐金属材料研究应集中在以下三个方面: 首先,研究各种涂层的成分、防护机理及提高耐蚀性能的方法; 加大涂层的实海试验,研究其在不同海洋环境下的腐蚀规律及失效形式,构建不同环境下的腐蚀模型,达到预测涂层使用寿命的目的。其次,研究喷涂参数对涂层耐腐蚀性能的影响,优化喷涂工艺参数,提高喷涂效率,降低涂层制备成本,提高涂层的耐腐蚀性能。最后,电弧喷涂过程中也会产生噪声、粉尘以及喷涂材料的浪费等问题,如何降低喷涂对环境的污染、研发高性能金属喷涂材料、提高喷涂材料利用率也应是未来一段时间的研究重点。
目前,国内电弧喷涂技术研发和应用发展迅猛,为国民经济快速发展做出了重要贡献,但电弧喷涂海洋防腐金属涂层的研究与发达国家仍存在较大差距。因此,迫切需要建立包括钢结构腐蚀失效分析、电弧喷涂参数优化和喷涂材料选取等在内的完整的工业体系,进一步提高电弧喷涂防腐金属涂层的性能,使得电弧喷涂技术在海洋腐蚀防护领域中发挥更加重要的作用。——论文作者:徐金勇,吴庆丹,魏新龙,肖金坤,张 超
参考文献
1 Yang Y X,Rob B,Brijan I,et al. Chemical Engineering & Processing Process Intensification,2012,51( 1) ,53.
2 Xu C,Zou W H,Yang Y M,et al. Journal of Natural Gas Geoscience, 2017,28( 8) ,1139.
3 Sharma R. Marine Technology Society Journal,2011,45( 5) ,28.
4 Drach A,Tsukrov I,Decew J,et al. Corrosion Science,2013,76( 10) , 453.
5 Odhiambo J G,Zhang L,Liu T,et al. Applied Mechanics & Materials, 2014,513-517,189.
6 Atashin S,Toloei A S. Journal of Materials Engineering & Performance, 2013,22( 7) ,2038.
7 Aspect I T,Tyron A. Journal of Mining,2013,2013( 6) ,1.
8 Moradi M,Song Z L,Yang L J,et al. Corrosion Science,2014,84( 3) ,